Comprehensive Guide to Industrial Electronic Equipment
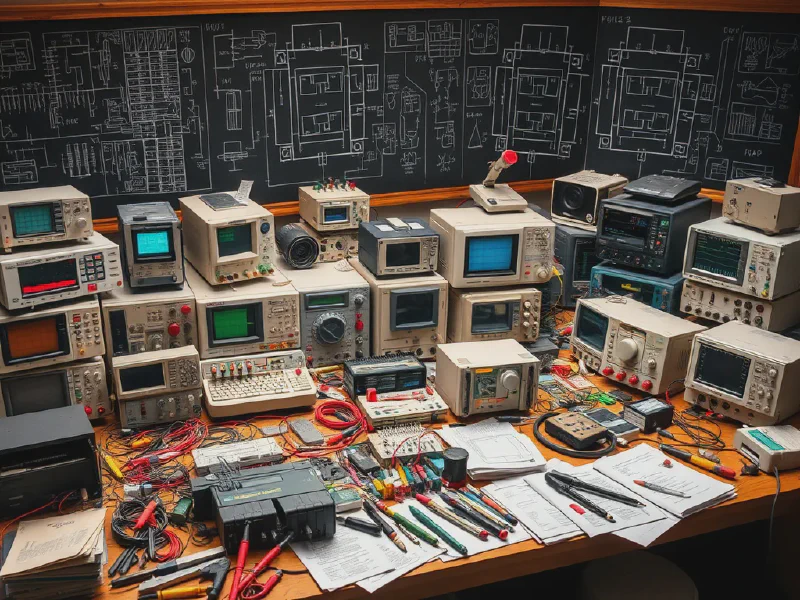
Understanding Industrial Electronic Equipment: An Essential Component in Modern Industry
Industrial Electronic Equipment plays a crucial role in the efficiency and effectiveness of contemporary manufacturing processes. This category of equipment integrates electronic components to automate, monitor, and control industrial operations. From assembly lines to sophisticated manufacturing systems, Industrial Electronic Equipment underpins the functionality of various sectors including automotive, food processing, and pharmaceuticals. The integration of electronics allows for precise control, enhanced safety, and improved productivity in industrial environments.
Using a pdf data logger enhances data accuracy and streamlines the monitoring process for various applications.
The significance of Industrial Electronic Equipment extends beyond mere automation. These systems are designed to enhance operational efficiency by minimizing human error, optimizing performance through data analysis, and streamlining communication between different manufacturing units. This technology encompasses a variety of devices that support industrial tasks, including sensors, programmable logic controllers (PLCs), and industrial robots, making it an indispensable component of modern industry.
As technology progresses, the types of Industrial Electronic Equipment are continuously evolving. Innovations in electronic design and embedded systems have led to the development of smarter and more flexible equipment. This adaptability is critical for meeting the diverse needs of industries, allowing for scalable solutions that can be tailored to specific operations. Advanced features, such as real-time monitoring and data integration with internet-based systems, have become common in modern electronic equipment, further enhancing its capabilities and reliability.
The implementation of Industrial Electronic Equipment is not only limited to manufacturing but also spans across various applications. Industries use these systems to improve quality control, enhance safety measures, and facilitate complex process automation. By leveraging electronic equipment, organizations can achieve higher output rates, reduce waste, and ensure compliance with stringent quality standards. The reliance on this technology underscores its fundamental role in driving industrial efficiency and competitiveness.
In summary, Industrial Electronic Equipment is a vital aspect of today’s industrial landscape, providing the necessary tools for automation, data processing, and effective resource management. As industries continue to face the pressures of increased productivity and reduced operational costs, the role of electronic equipment is set to expand, paving the way for further advancements and improved manufacturing strategies.
A silicone keyboard provides durability and easy cleaning, making it ideal for busy work environments.
Types of Industrial Electronic Equipment
One of the primary types of Industrial Electronic Equipment includes Programmable Logic Controllers (PLCs). PLCs serve as the brain of industrial automation, offering flexibility and reliability in controlling machinery. They can be programmed to carry out specific functions depending on the operational requirements of a facility, making them highly versatile solutions that can adapt to changes in processes and technologies.
Another key category of Industrial Electronic Equipment is industrial sensors and transducers. These devices are critical for collecting data on various parameters such as temperature, pressure, and flow rates. By providing real-time feedback on the status of manufacturing processes, sensors enable operators to make informed decisions and maintain optimal operating conditions.
Industrial robots and automation devices also represent a significant segment of Industrial Electronic Equipment. These advanced machines automate repetitive tasks, improving both efficiency and safety. By utilizing robotic systems, industries can enhance their production capabilities while reducing the risk of workplace injuries associated with manual operations.
With a 3 phase power logger, engineers can efficiently diagnose electrical issues and optimize system performance.
Applications of Industrial Electronic Equipment
In the realm of manufacturing processes, Industrial Electronic Equipment is foundational. Through automation and control systems, industries can streamline production lines, increase output, and enhance the overall efficiency of operations. The ability to precisely manage machinery and workflows results in reduced downtime and improved consistency in product quality.
Process automation is another critical application of Industrial Electronic Equipment. By integrating electronic systems with manufacturing practices, industries can achieve significant improvements in control and precision. Automated processes can run continuously, often with minimal human intervention, which in turn maximizes productivity and reduces operational costs.
Quality control systems heavily rely on Industrial Electronic Equipment to maintain standards and enforce compliance. With electronic inspection tools and measurement devices, companies can conduct rigorous testing and monitoring of products during production. This ensures that only high-quality items reach the market and helps prevent costly recalls due to defects.
Maintenance of Industrial Electronic Equipment
Preventive maintenance techniques are essential for ensuring the longevity and efficacy of Industrial Electronic Equipment. Regular inspections, cleaning, and scheduled servicing can help identify potential issues before they lead to equipment failure. Implementing a preventive maintenance program not only extends the life of the equipment but also ensures consistent operational performance.
Troubleshooting common issues is another important aspect of maintaining Industrial Electronic Equipment. Technical personnel must be trained to diagnose problems quickly and accurately to minimize downtime. Familiarity with common faults and their resolutions can significantly enhance an organization’s ability to maintain productivity.
Calibration and testing procedures are vital in ensuring that Industrial Electronic Equipment operates within specified parameters. Regular calibration of sensors and controllers guarantees accurate measurements and control, which is crucial for maintaining production quality and safety standards.
Safety Protocols in Industrial Electronics
Electrical safety standards are integral to the effective operation of Industrial Electronic Equipment. Compliance with regulations such as the National Electrical Code (NEC) ensures safe installation and operation of electronic systems, reducing the risk of electrical hazards and accidents in the workplace.
Hazardous area equipment guidelines are essential for industries working in environments where flammable gases and dust are present. Specific equipment must be utilized to prevent explosions and ensure safety for workers and assets in such dangerous settings. This includes utilizing explosion-proof enclosures and intrinsically safe designs.
Personal protective equipment (PPE) plays a crucial role in safeguarding individuals working with or near Industrial Electronic Equipment. Ensuring that workers have access to appropriate PPE, such as insulated gloves, goggles, and protective clothing, is vital in promoting safety and preventing injuries in industrial environments.
Innovations in Industrial Electronic Equipment
Smart manufacturing and IoT integration represent a transformative trend in Industrial Electronic Equipment. By connecting machines and systems through the Internet of Things (IoT), industries can achieve unprecedented levels of data exchange and communication. This connectivity enables real-time monitoring, predictive maintenance, and enhanced decision-making capabilities.
Advancements in industrial robotics are also shaping the future of Industrial Electronic Equipment. Sophisticated robots with artificial intelligence capabilities are becoming more common, allowing for more complex tasks to be performed with higher efficiency. These innovations are changing the landscape of production and enabling manufacturers to adapt to the demands of changing markets.
Energy-efficient equipment solutions are crucial as industries seek to reduce their carbon footprint and operating costs. New technologies focus on optimizing energy consumption, enhancing the sustainability of industrial operations, and decreasing operational expenses through innovative design and advanced control systems.